Manutenção Preventiva em Compressores Parafuso
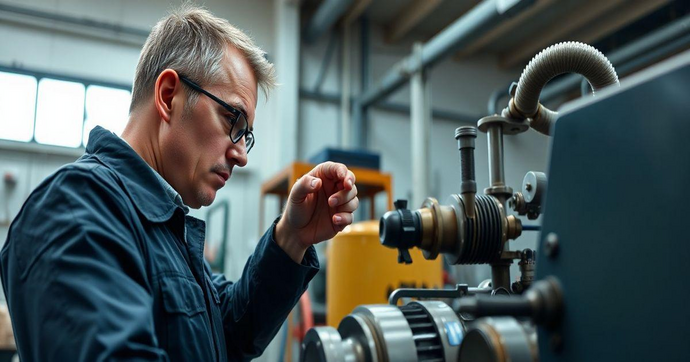
Por: Larissa - 24 de Dezembro de 2024
A manutenção preventiva compressor parafuso é essencial para garantir o funcionamento eficiente e prolongar a vida útil desses equipamentos. Neste artigo, vamos explorar o que é a manutenção preventiva, seus benefícios, e como realizá-la de forma eficaz. Você também aprenderá sobre a frequência ideal para as manutenções e os sinais que indicam a necessidade de atenção especial. Continue lendo e descubra como manter seu compressor sempre em ótimas condições.
O que é manutenção preventiva em compressores parafuso
A manutenção preventiva em compressores parafuso refere-se a um conjunto de práticas e procedimentos que têm como objetivo garantir o funcionamento eficiente e seguro desse tipo de equipamento. Este tipo de compressor é amplamente utilizado em indústrias que exigem uma fonte de ar comprimido constante e confiável. Devido à sua importância, a implementação de um programa de manutenção preventiva se torna fundamental para evitar falhas inesperadas e garantir a continuidade das operações.
A manutenção preventiva envolve inspeções regulares, ajustes, limpezas e substituições de peças antes que ocorra uma falha. Isso significa que os problemas são resolvidos antes de se tornarem críticos, reduzindo assim o risco de paradas inesperadas na linha de produção. Uma abordagem preventiva ajuda a identificar e corrigir pequenos problemas, o que pode economizar tempo e dinheiro no longo prazo.
Os compressores parafuso utilizam rotors que giram para comprimir o ar, proporcionando uma operação contínua e eficiente. Por serem máquinas complexas, eles necessitam de cuidados específicos. A manutenção preventiva pode incluir a verificação de peças essenciais, como o filtro de ar, óleo, correias, e a manutenção do sistema de lubrificação. Essa prática ajuda não só na eficiência do compressor, mas também na preservação da qualidade do ar comprimido.
Uma das principais metas da manutenção preventiva é minimizar os custos de operação e maximizar a vida útil do equipamento. Quando a manutenção é bem executada, a probabilidade de falhas catastróficas diminui consideravelmente. Assim, as indústrias podem se concentrar em suas atividades principais sem se preocupar com problemas inesperados relacionados ao ar comprimido.
Não é apenas a eficiência que é melhorada através da manutenção preventiva; a segurança dos operadores também é um fator importante. Compressores que não recebem manutenção regular podem desenvolver vazamentos ou outros problemas que podem representar riscos à segurança de quem opera ou trabalha próximo ao equipamento. Por isso, seguir um cronograma de manutenção preventiva é fundamental para garantir que todos os aspectos do funcionamento do compressor estejam dentro das normas de segurança.
A frequência e o tipo de manutenção dependem do uso do equipamento e das recomendações do fabricante. Alguns compressores podem precisar de manutenções mais frequentes em comparação a outros, especialmente se estiverem operando em ambientes hostis ou sujeitos a altas cargas. Por isso, é necessário um planejamento adequado para assegurar que todas as etapas de manutenção sejam executadas de forma eficaz.
Além disso, muitas empresas optam por um sistema de monitoramento que acompanha o desempenho do compressor. Isso permite que os operadores identifiquem anomalias e problemas emergentes com mais facilidade. Alertas automáticos podem ser recebidos, sinalizando a necessidade de manutenção antes que um problema maior ocorra, oferecendo uma solução proativa em vez de reativa.
Outro benefício da manutenção preventiva é a possibilidade de realizar serviços em um momento conveniente, minimizando impactos nas operações do dia a dia. Quando a manutenção é agendada, as empresas podem planejar paradas programadas, evitando assim prejuízos que poderiam ocorrer devido a um desligamento inesperado do equipamento.
Por fim, a manutenção preventiva também pode aumentar a eficiência energética do compressor. Compressores que não são mantidos adequadamente podem operar de maneira ineficiente, exigindo mais energia para funcionar. Isso não apenas aumenta os custos operacionais, mas também contribui para um maior impacto ambiental. Um compressor bem mantido opera de forma mais eficiente, resultando em economia de energia e redução de emissões de carbono.
Se você está considerando a possibilidade de alugar um equipamento para atender suas necessidades, você pode conferir opções de aluguel de compressor de ar e garantir que suas operações tenham acesso à tecnologia de ponta, além de poder contar com manutenção programada desde o início.
Em resumo, a manutenção preventiva em compressores parafuso é crucial para assegurar uma operação eficiente, segura e econômica. Com inspeções regulares e práticas adequadas, é possível evitar falhas e prolongar a vida útil do equipamento, beneficiando diretamente os processos produtivos das indústrias que dependem desse tipo de compressor.
Benefícios da manutenção preventiva
A manutenção preventiva é uma prática recomendada para garantir o desempenho ideal dos equipamentos, especialmente em sistemas complexos como compressores parafuso. Implementar um programa eficaz de manutenção preventiva traz uma série de benefícios significativos que podem impactar positivamente tanto a eficiência operacional quanto a saúde financeira de uma empresa. Neste texto, vamos explorar os principais benefícios dessa prática.
Um dos principais benefícios da manutenção preventiva é a redução do tempo de inatividade do equipamento. Quando os compressores são mantidos regularmente, a probabilidade de falhas inesperadas diminui. Isso significa menos paradas não programadas, que podem atrasar a produção e gerar perdas financeiras. Em ambientes industriais onde o tempo é um fator crítico, essa redução de inatividade se traduz em economia significativa de custos e aumento da produtividade.
Além disso, a manutenção preventiva promove a longevidade do equipamento. Os compressores parafuso, quando submetidos a uma rotina adequada de cuidados, tendem a durar mais. Isso significa que o investimento inicial em um compressor é maximizado, já que sua vida útil é estendida. A manutenção adequada garante que os componentes essenciais estejam sempre funcionando de maneira ideal, o que evita a necessidade de substituições frequentes e onerosas.
Outro benefício notável é a melhoria da eficiência energética. Compressores que não recebem manutenção adequada podem operar de forma ineficiente, consumindo mais energia do que o necessário. Através da manutenção preventiva, é possível identificar e corrigir problemas que afetam a eficiência, resultando em um menor consumo de energia elétrica. Isso não apenas reduz os custos operacionais, mas também ajuda a empresa a ser mais sustentável, contribuindo para a redução das emissões de carbono.
Adicionalmente, a manutenção preventiva assegura a qualidade do ar comprimido gerado. Em muitos setores, a qualidade do ar comprimido é crítica, pois pode impactar diretamente a qualidade dos produtos finais. Através da regularidade na manutenção, é possível garantir que filtros e separadores estejam em boas condições, evitando a contaminação do ar. Isso se traduz em um melhor desempenho dos produtos e em uma menor taxa de rejeição.
A segurança operacional também é um aspecto fundamental que se beneficia da manutenção preventiva. Compressores mal mantidos podem se tornar riscos à segurança, levando a acidentes e ferimentos. Problemas como vazamentos de ar, falhas nos sistemas de lubrificação e superaquecimento são menos prováveis quando um programa de manutenção apropriado é seguido. Garantir a segurança dos operadores e do ambiente de trabalho deve ser uma prioridade, e a manutenção preventiva é uma ferramenta vital para alcançar essa meta.
Outro ponto a destacar é que a manutenção preventiva pode proporcionar uma melhor previsibilidade nos custos. Ao invés de enfrentar despesas inesperadas relacionadas a falhas e reparos emergenciais, as empresas podem planejar e orçar as manutenções de forma mais estratégica. Isso é especialmente importante para empresas que operarão com orçamento fixo, pois permite um melhor gerenciamento dos recursos disponíveis.
A capacidade de planejar manutenções também facilita a logística operacional. Ao saber quando um compressor precisará de manutenção, as empresas podem programar paradas em momentos que minimizam o impacto nas operações. Isso oferece controle sobre o cronograma de produção e garante que as interrupções ocorram de forma a perpetuar a eficiência operacional.
Adicionalmente, a implementação de um programa de manutenção preventiva pode contribuir para um ambiente de trabalho mais motivador. Quando os funcionários sabem que estão trabalhando em um ambiente seguro e que as máquinas são confiáveis, a moral e a produtividade tendem a aumentar. A confiança na operação dos equipamentos se traduz em um equipe mais engajada e focada em resultados positivos.
Por fim, se sua empresa está considerando opções para suprir a necessidade de ar comprimido de forma eficiente e econômica, a locação de compressores de ar pode ser uma excelente alternativa. Com essa opção, você pode acessar equipamentos modernos e bem mantidos, economizando tempo e dinheiro em manutenção.
Em resumo, os benefícios da manutenção preventiva vão muito além da simples manutenção de máquinas. Ela oferece melhorias na eficiência operacional, segurança, qualidade do produto e economia de custos, criando um ambiente produtivo e seguro para todos os envolvidos. É um investimento que compensa a longo prazo, proporcionando tranquilidade e segurança para as operações diárias.
Principais componentes do compressor parafuso
Os compressores parafuso são equipamentos complexos que desempenham um papel crucial em diversas operações industriais. A compreensão dos principais componentes que compõem esses dispositivos é essencial para garantir seu funcionamento adequado e a manutenção preventiva necessária. Este tipo de compressor é projetado para oferecer eficiência e confiabilidade, e seus componentes trabalham em conjunto para atingir esses objetivos.
O primeiro componente a ser destacado é o par de rotores. Os rotores são a parte fundamental do compressor parafuso e são responsáveis pela compressão do ar. Geralmente, são constituídos de um rotor macho e um rotor fêmea, que giram em direções opostas. À medida que os rotores giram, o ar é capturado e, ao mesmo tempo, comprimido em um espaço cada vez menor, resultando em um aumento significativo na pressão do ar. A precisão na fabricação desses rotores é vital para a eficiência do compressor e para evitar vazamentos de ar comprimido.
Outro componente importante é o sistema de lubrificação. O lubrificante é essencial para reduzir o atrito entre as partes móveis do compressor, aumentando sua durabilidade e eficiência. Ele também serve para resfriar os rotores e outros componentes, prevenindo o superaquecimento. Existem diversos tipos de lubrificantes, e a escolha do adequado é fundamental para manter as propriedades do compressor e prolongar sua vida útil. Realizar a manutenção compressor de ar regular garante que o sistema de lubrificação funcione de maneira eficaz.
O reservatório de ar é outro componente crítico do compressor parafuso. Ele armazena o ar comprimido gerado, permitindo um fornecimento contínuo e constante de ar para as aplicações. Este reservatório evita flutuações de pressão, proporcionando uma operação mais estável. Além disso, ele desempenha um papel na separação de umidade e impurezas do ar comprimido, garantindo que o ar seja de alta qualidade. A manutenção periódica do reservatório é essencial para evitar corrosão e acúmulo de água, o que pode comprometer a eficiência do sistema.
A válvula de descarga é um componente que controla a pressão do ar comprimido que sai do compressor. Essa válvula é crucial para a segurança do equipamento, pois evita que a pressão dentro do sistema atinja níveis perigosos. Em situações de sobrepressão, a válvula de descarga se abre automaticamente para liberar o excesso de pressão, protegendo o compressor e os demais componentes do sistema. A verificação regular desta válvula é importante para assegurar que ela funcione corretamente quando necessário.
O filtro de ar também desempenha uma função vital no funcionamento do compressor parafuso. Ele tem a tarefa de remover partículas sólidas e contaminantes do ar utilizado no processo de compressão. Um filtro de ar limpo contribui para a qualidade do ar comprimido, bem como para a proteção dos componentes internos do compressor. Os filtros devem ser monitorados e trocados de acordo com as recomendações do fabricante, evitando assim a obstrução e o comprometimento do desempenho do compressor.
Além disso, o sistema de controle eletrônico é responsável pela automação do funcionamento do compressor. Ele monitora parâmetros como temperatura, pressão e níveis de óleo, garantindo que o equipamento opere dentro das condições ideais. Em alguns modelos, sistemas avançados de controle podem fornecer dados em tempo real, permitindo que os operadores tenham uma visão geral do desempenho do compressor. Isso facilita a identificação de possíveis problemas antes que se tornem críticos, permitindo que a manutenção seja programada de maneira eficiente.
O cooler é outro componente importante que contribui para a eficiência do compressor parafuso. Ele atua no resfriamento do ar comprimido após o processo de compressão, reduzindo sua temperatura antes que seja enviado para o reservatório de ar. O resfriamento adequado ajuda a prevenir problemas de superaquecimento e garante que o ar comprimido esteja em temperatura adequada para suas aplicações finais.
Por último, mas não menos importante, o ponto de ajuste e controle de pressão é essencial para a operação do compressor. Este ponto permite que os operadores ajustem a pressão de saída do compressor para atender às necessidades específicas das aplicações. Um controle preciso da pressão é essencial em processos industriais, onde a inconsistente pode levar a falhas e desperdícios.
Compreender os principais componentes do compressor parafuso e suas funções não só ajuda a otimizar seu desempenho, mas também facilita a execução de manutenções adequadas. Garantir que cada um desses componentes esteja em bom estado é vital para assegurar uma operação eficiente e segura do compressor, proporcionando resultados otimais para as indústrias que dependem desse tipo de equipamento.
Como realizar a manutenção preventiva
A realização de manutenção preventiva em compressores de ar, especialmente em compressores parafuso, é fundamental para garantir eficiência e prolongar a vida útil do equipamento. O processo envolve uma série de etapas específicas que devem ser seguidas regularmente para evitar falhas e se assegurar de que o equipamento esteja sempre em ótima condição de funcionamento. Neste artigo, abordaremos como realizar a manutenção preventiva, seguindo práticas recomendadas e diretrizes essenciais.
O primeiro passo para uma manutenção preventiva eficaz é ter um plano de manutenção bem estruturado. Esse plano deve incluir um cronograma das atividades a serem realizadas, responsáveis por cada tarefa, e os intervalos adequados para a execução de cada manutenção. É importante seguir as recomendações do fabricante, que geralmente fornecem orientações específicas sobre a frequência da manutenção e as tarefas a serem realizadas. Para compressores como o compressor de ar parafuso 30 hp, ter um plano definido é essencial para assegurar que tudo funcione corretamente.
Uma parte essencial da manutenção preventiva é a inspeção visual do equipamento. Isso deve incluir a verificação de componentes como mangueiras, conexões, e peças móveis. A inspeção ajuda a identificar sinais de desgaste, vazamentos ou danos que possam comprometer a operação. Qualquer anomalia deve ser imediatamente relatada e corrigida. A realização de uma inspeção visual regular pode evitar problemas maiores no futuro, além de garantir a segurança dos operadores.
Outra etapa importante é a substituição dos filtros de ar e óleo conforme a necessidade. Os filtros desempenham um papel crucial na purificação do ar que é comprimido e, no caso do óleo, mantêm o sistema de lubrificação funcionando adequadamente. Filtros entupidos podem causar uma série de problemas, incluindo a redução do fluxo de ar e a sobrecarga do motor. Para garantir que o compressor opere de forma eficiente, os filtros devem ser inspecionados e trocados regularmente, seguindo as recomendações do fabricante.
A verificação do nível de óleo é uma parte essencial da manutenção preventiva. O óleo é responsável por reduzir o atrito entre as partes móveis e resfriar o sistema. Portanto, é importantíssimo garantir que o nível de óleo esteja adequado. Caso contrário, o compressor pode operar em temperaturas mais altas, resultando em danos à maquinaria. Use sempre o tipo de óleo recomendado pelo fabricante e substitua-o em conformidade com o cronograma estabelecido.
O sistema de refrigeração também deve ser monitorado. Compressores parafuso geram calor durante a operação, e um sistema de resfriamento eficaz é vital para evitar o superaquecimento. Verifique periodicamente o funcionamento do cooler e a presença de sujeira ou bloqueios que possam impedir a passagem de ar. Uma limpeza regular desses componentes é fundamental para assegurar que o sistema de refrigeração esteja operando de maneira eficaz.
Além disso, é recomendável realizar testes de pressão e vazamento regularmente. Isso envolve checar se existem vazamentos no sistema de ar comprimido, já que a perda de ar pode resultar em desperdício de energia e aumento dos custos operacionais. Caso sejam encontrados vazamentos, é essencial corrigir imediatamente a situação, pois mesmo pequenos vazamentos podem ter um impacto significativo na eficiência do sistema.
Uma parte crucial da manutenção preventiva é o treinamento dos operadores. Operadores bem treinados são mais capazes de identificar problemas e realizar procedimentos de manutenção simples. O treinamento deve incluir não apenas como operar o compressor, mas também como realizar inspeções visuais e quando comunicar a necessidade de manutenção. Um operador informado pode ajudar a prolongar a vida útil do equipamento e reduzir a frequência de reparos.
Além disso, a documentação da manutenção realizada é fundamental. Ao manter registros detalhados de todas as atividades de manutenção, você consegue monitorar o desempenho do compressor ao longo do tempo. Esses registros também ajudam na identificação de padrões que podem indicar a necessidade de atenção especial em determinados componentes ou sistemas. Isso pode facilitar as decisões sobre futuras manutenções e investimentos em equipamentos.
Por fim, a realização de manutenções corretivas deve ser sempre acompanhada de perto. Se um problema surgir, é essencial resolver a questão rapidamente em vez de esperar. O tempo e o esforço investidos na manutenção preventiva geralmente resultam em economias substanciais em reparos emergenciais e tempo de inatividade.
Em resumo, a manutenção preventiva é uma prática que exige atenção e planejamento, mas os benefícios são significativos. Com um bom plano de manutenção, inspeções regulares e um compromisso com o treinamento, as empresas podem garantir que seus compressores parafuso operem de maneira eficaz e segura. Dessa forma, a eficiência, a durabilidade e a segurança podem ser maximizadas, trazendo resultados positivos para as operações industriais em geral.
Frequência ideal para manutenção preventiva
A manutenção preventiva é uma prática essencial para garantir o funcionamento eficiente e seguro dos compressores, especialmente os do tipo parafuso. No entanto, um aspecto crítico dessa manutenção é a sua frequência. Realizar a manutenção na periodicidade correta não só assegura que os equipamentos operem de maneira ideal, mas também prolonga sua vida útil e evita falhas inesperadas. Neste artigo, discutiremos a frequência ideal para a manutenção preventiva e como estabelecê-la de maneira eficaz.
Em geral, a frequência da manutenção preventiva pode variar com base em diversos fatores, incluindo o tipo de compressor, as condições de operação e os requisitos do fabricante. Portanto, não existe uma “receita única” para todos os compressores. É crucial seguir as recomendações do fabricante, que geralmente fornecem diretrizes específicas sobre a periodicidade das manutenções. Isso garante que o equipamento permaneça dentro das especificações adequadas e evita problemas durante a operação.
Uma diretriz comum sugere que a manutenção preventiva deve ser realizada a cada 500 a 1.000 horas de operação, dependendo do modelo e das condições em que o compressor está sendo utilizado. Para um compressor que opera em um ambiente normal, condicionantes como a qualidade do ar, temperatura e umidade também são fatores a serem considerados. Compressores que operam em ambientes severos, com altos níveis de poeira ou umidade, podem necessitar de manutenções mais frequentes.
Além das horas de operação, a frequência de manutenção também deve considerar as condições de uso. Por exemplo, se o compressor estiver em funcionamento contínuo ou se for utilizado em ciclos de carga pesada, uma manutenção mais frequente é recomendada. Nesses casos, pode ser apropriado realizar inspeções a cada 250 horas de operação. Isso pode ajudar a detectar quaisquer problemas precocemente, evitando que se tornem falhas sérias que exigiriam reparos extensos.
Outra consideração importante diz respeito ao tipo de manutenção que está sendo realizada. As manutenções gerais, que incluem trocas de filtros, verificação de níveis de óleo e inspeções visuais, devem ser mais frequentes do que a manutenção de componentes mais complexos, como o par de rotores ou o sistema de refrigeração. Manutenções menores podem ser programadas trimestralmente, enquanto manutenções mais abrangentes podem ser realizadas semestralmente ou anualmente, dependendo da condição do compressor e das recomendações do fabricante.
A documentação adequada é um fator crucial para determinar a frequência ideal da manutenção preventiva. Ao manter um registro detalhado de todas as atividades realizadas, incluindo a data, tipo de manutenção e quaisquer anotações sobre o desempenho do equipamento, as empresas podem obter uma visão clara de quando a manutenção se torna necessária. Esse histórico ajuda a identificar tendências, permitindo que os operadores realizem ajustes para garantir que as manutenções estejam em conformidade com as necessidades do compressor.
Cabe ressaltar que a avanço tecnológico também tem influenciado a maneira como as manutenções preventivas são programadas. Sistemas modernos de monitoramento e automação podem fornecer dados em tempo real sobre o desempenho do compressor, alertando os operadores sobre a necessidade de intervenções e permitindo uma programação mais precisa para manutenção preventiva. Esses sistemas ajudam a garantir que as manutenções sejam realizadas no momento certo e de maneira eficiente, reduzindo a probabilidade de falhas inesperadas.
Em adição, o treinamento dos operadores é um fator significativo na determinação da frequência da manutenção preventiva. Operadores bem treinados são mais propensos a identificar problemas antes que se tornem graves. Isso pode significar que ajustes na frequência de manutenção preventiva sejam feitos com base na experiência e no julgamento dos operadores, desde que acompanhados de perto e documentados.
Algumas empresas optam por implementar um sistema de manutenções baseadas em condições, ao invés de seguir um calendário fixo. Isso significa que a frequência da manutenção preventiva é ajustada de acordo com os resultados das inspeções regulares e do desempenho geral do equipamento. Embora essa abordagem possa ser mais eficiente em termos de custos, ela requer um compromisso significativo com monitoramento e testes constantes. Para muitas organizações, a implementação de um sistema baseado em condições pode ser mais eficaz e satisfatória a longo prazo.
Finalmente, não se deve esquecer da importância das manutenções corretivas. Quando um problema é detectado, é essencial que o equipamento seja atendido imediatamente. Isso significa que a manutenção corretiva deve ser realizada em conjunto com a manutenção preventiva; como tal, ajustes na frequência das atividades preventivas podem ser feitos em resposta a falhas que ocorreram no passado.
Em resumo, a frequência ideal para a manutenção preventiva de compressores parafuso varia em função de diversos fatores, incluindo as recomendações do fabricante, as condições de operação, o tipo de uso e a documentação realizada. Com um planejamento adequado e uma abordagem baseada em regras e condições, as empresas podem otimizar a performance de seus compressores, minimizando custos operacionais e garantindo uma operação eficiente e segura.
Erros comuns a evitar na manutenção
A manutenção preventiva em compressores parafuso é fundamental para garantir a eficácia e a longevidade dos equipamentos. No entanto, muitos profissionais cometem erros que podem comprometer a performance dos compressores e gerar custos desnecessários. Neste artigo, vamos discutir alguns dos erros comuns que devem ser evitados durante a manutenção para assegurar que os compressores funcionem de maneira ideal.
Um dos principais erros a evitar é negligenciar o cronograma de manutenção. Muitas vezes, por conta da rotina agitada de uma empresa, a manutenção preventiva pode ser deixada para depois ou até mesmo esquecida. Ignorar a necessidade de realizar manutenções programadas pode levar a falhas inesperadas e interrupções na produção, que podem resultar em custos elevados e tempo de inatividade. É crucial que as empresas estabeleçam um cronograma de manutenção e se comprometam a cumpri-lo, mesmo quando a operação está estável.
Além disso, o uso inadequado de peças de reposição também é um erro comum. Em um esforço para reduzir custos, algumas organizações podem optar por peças de qualidade inferior ou não compatíveis com os padrões do equipamento. A utilização de peças inadequadas pode resultar em falhas ainda mais sérias e em danos aos componentes do compressor. Sempre que realizar manutenções, utilize peças de reposição recomendadas pelo fabricante para garantir a compatibilidade e a eficácia.
Outro erro frequente é a falta de atenção aos detalhes durante as inspeções. Manutenção significa muito mais do que apenas trocar filtros ou óleo; envolve uma análise minuciosa de cada componente do compressor. Durante as inspeções, os técnicos devem estar atentos a sinais visíveis de desgaste, vazamentos de ar e outros problemas que podem não ser imediatamente evidentes. Não identificar e abordar essas questões de forma adequada pode levar a problemas maiores no futuro. Portanto, ao realizar as inspeções, não apresse o processo e certifique-se de que todas as partes estão verificadas de maneira eficaz.
Um erro grave que pode ocorrer é não documentar as atividades de manutenção. O registro detalhado de todas as manutenções realizadas é vital para o gerenciamento eficaz dos compressores. Sem documentação, será impossível acompanhar o histórico do equipamento, identificar padrões de falhas ou mesmo saber quando e quais manutenções foram executadas. Criar e manter um registro organizado não apenas ajuda na análise do desempenho do compressor, mas também é essencial para planejamento futuro e tomada de decisões informadas.
Adicionalmente, muitos operadores e técnicos cometem o erro de não seguir as recomendações do fabricante. Cada compressor vem com um guia específico de manutenção que inclui informações sobre frequências e tipos de serviços necessários. Ignorar essas diretrizes pode levar a uma manutenção inadequada, que não atenderá às necessidades do compressor, resultando em falhas e degradação no desempenho. Sempre consulte o manual do proprietário do compressor e siga as recomendações para garantir a longevidade e o funcionamento adequado do equipamento.
Outro erro comum é a falta de treinamento adequado dos operadores. Funcionários que não estão bem treinados podem não identificar problemas em potencial ou podem não realizar a manutenção corretamente. Isso não só pode criar riscos para a segurança, mas também pode comprometer a eficiência do compressor. As empresas devem investir em treinamento contínuo para seus técnicos e operadores, garantindo que todos estejam cientes das melhores práticas e procedimentos de manutenção.
A não realização de manutenções corretivas de maneira oportuna é uma armadilha que deve ser evitada. Quando um problema é identificado, a manutenção deve ser tratada imediatamente. Ignorar pequenos problemas pode levar a falhas maiores que exigem reparos mais extensos e custosos. Assim, se um operador notar um vazamento de ar, uma mudança no desempenho ou qualquer outro sinal de alerta, é fundamental agir rapidamente e realizar as correções necessárias o quanto antes.
Muitos profissionais também cometem o erro de não monitorar a qualidade do ar comprimido. A qualidade do ar é crítica, especialmente em aplicações sensíveis, e variações podem comprometer a integridade dos produtos finais. Isso pode acontecer devido à falta de filtragem ou à presença de umidade no sistema. Portanto, é importante implementar um sistema de monitoramento que avalie continuamente a qualidade do ar comprimido, assim como realizações de manutenções nos filtros e separadores adequados.
Por fim, outro erro comum é a subestimação da importância da segurança. Manutenções preventivas devem ser realizadas seguindo as melhores práticas de segurança. Isso inclui o uso de equipamentos de proteção individual (EPIs), bem como a disposição adequada de ferramentas e peças durante o trabalho. Ignorar esses aspectos pode resultar em acidentes e colocar a segurança dos trabalhadores em risco.
Em resumo, evitar esses erros comuns na manutenção de compressores parafuso pode fazer uma grande diferença na eficiência, segurança e prolongamento da vida útil do equipamento. Ao seguir as práticas adequadas de manutenção, documentar tudo, treinar os operadores e se comprometer com a rotina de manutenções, as empresas podem garantir um desempenho confiável e econômico, reduzindo custos e aumentando a confiabilidade operacional.
Sinais de que seu compressor precisa de manutenção
Os compressores de ar, especialmente os do tipo parafuso, são componentes cruciais para muitas operações industriais. Entretanto, como qualquer equipamento mecânico, eles estão sujeitos a desgastes e podem enfrentar problemas ao longo do tempo. Reconhecer os sinais de que seu compressor precisa de manutenção é fundamental para evitar falhas mais graves, reduzir o tempo de inatividade e garantir a eficiência operacional. Neste artigo, discutiremos os principais sinais que indicam que seu compressor precisa de atenção.
Um dos sinais mais evidentes de que seu compressor precisa de manutenção é um desempenho irregular. Se o compressor não está gerando a pressão esperada ou se os níveis de ar comprimido estão inconsistentes, isso pode indicar problemas internos. Fatores como vazamentos, filtros obstruídos ou falhas no sistema de lubrificação podem afetar a pressão do ar comprimido. Se você perceber variações na pressão, é fundamental realizar uma inspeção detalhada no equipamento.
A presença de ruídos incomuns também é um sinal que você não deve ignorar. Uma operação normal de um compressor deve ser relativamente silenciosa. Ruídos excessivos, como batidas, zumbidos ou rangidos, podem indicar que há peças soltas, rolamentos danificados ou outros problemas mecânicos. Se o compressor começar a emitir sons estranhos, é uma boa prática parar o equipamento e investigar a origem do problema antes que se torne mais sério.
Além disso, vazamentos de óleo ou ar são alertas claros de que algo não está certo. O óleo é essencial para o funcionamento adequado do compressor, pois lubrifica as partes móveis e reduz o atrito. Vazamentos podem indicar problemas nas conexões, mangueiras ou até mesmo nas vedações do equipamento. Igualmente, vazamentos de ar comprimido não são apenas uma questão de eficiência; eles também podem aumentar significativamente os custos operacionais. Caso identifique vazamentos, é importante agir rapidamente para efetuar reparos.
A temperatura elevada também é um sinal claro de que seu compressor precisa de atenção. O funcionamento normal de um compressor deve ocorrer dentro de faixas de temperatura adequadas. Se o equipamento está superaquecendo, isso pode indicar problemas no sistema de refrigeração, como falhas no cooler, bloqueios ou níveis de óleo abaixo do ideal. A operação de um compressor a temperaturas elevadas não só afeta seu desempenho, mas também pode causar danos permanentes ao equipamento.
A qualidade do ar comprimido é outro fator a ser levado em conta. Se você perceber que a qualidade do ar gerado pelo compressor está comprometida, como em casos onde o ar apresenta umidade excessiva ou contaminação, isso pode comprometer não apenas o funcionamento do próprio compressor, mas também os processos industriais que dependem desse ar. Filtros sujos ou inadequados e separadores de água estão entre as causas mais comuns de problemas relacionados à qualidade do ar comprimido. Se isso ocorrer, uma manutenção imediata deve ser realizada.
Outro indicativo importante é a dificuldade para iniciar o compressor. Se o equipamento tem dificuldade para ligar ou falha ao tentar iniciar, isso pode ser um sinal de falhas no motor, sistemas elétricos ou problemas no sistema de controle. É crucial investigar a causa raiz desse problema rapidamente para evitar uma possível falha total do equipamento.
A vibração excessiva é um outro sinal de alerta que não deve ser ignorado. O funcionamento eficiente de um compressor deve ser relativamente estável, e vibrações excessivas podem indicar que algo está desalinhado ou danificado. Isso pode estar relacionado a problemas nos rotores, nos mancais ou até mesmo em componentes elásticos do sistema. Se você notar vibrações incomuns, é vital interromper a operação e investigar o problema.
Além disso, uma redução na eficiência energética é um sinal importante de que o compressor pode precisar de manutenção. Se você notar que o consumo de energia aumentou sem justificativa, pode ser um indicativo de que o compressor não está operando de forma eficiente. Uma queda no desempenho pode resultar em um desperdício significativo de energia, impactando diretamente nos custos de operação. Inspecionar e ajustar os componentes alavancados para eficiência pode ser necessário.
Finalmente, a luminosidade no painel de controle é outro sinal que exige atenção. Muitos compressores modernos têm sistemas de monitoramento que incluem luzes indicadoras para diferentes alertas. Se qualquer luz de alerta estiver acesa, isso indica que há necessidade de atenção. Seja uma luz de pressão baixa, temperatura alta ou um aviso de falha, é importante consultar o manual e agir conforme as instruções apresentadas.
Em resumo, identificar os sinais de que seu compressor precisa de manutenção é vital para garantir a continuidade das operações industriais e a eficiência do equipamento. Ao prestar atenção em fatores como desempenho irregular, vazamentos, ruídos incomuns, temperatura elevada e qualidade do ar, você poderá detectar problemas antes que eles se tornem sérios. Manter um cronograma de manutenção preventiva e um monitoramento constante pode minimizar custos e aumentar a vida útil do seu compressor. Lembre-se, a atenção rápida a esses sinais não apenas protegem seu investimento, mas também garantem um ambiente de trabalho seguro e eficiente.
Quando chamar um especialista em manutenção
A manutenção de um compressor de ar é uma tarefa essencial para a operação de muitas indústrias, mas existem momentos em que a intervenção de um especialista se torna imprescindível. Compreender quando chamar um especialista pode ajudar a evitar reparos dispendiosos, minimizar o tempo de inatividade e garantir que seu equipamento funcione com eficiência. Neste artigo, abordaremos as situações mais comuns que indicam a necessidade de um especialista em manutenção.
Um dos principais sinais de que é hora de chamar um especialista é quando você percebe problemas complexos de desempenho. Se o seu compressor não estiver alcançando a pressão desejada, gerando menos ar comprimido do que o normal ou apresentando flutuações de pressão, pode ser um indicativo de falhas internas que requerem diagnósticos sofisticados. Mesmo que você tenha conhecimento básico sobre compressors, alguns problemas envolvem componentes que podem exigir ferramentas e análises avançadas que apenas um especialista pode realizar.
Outro sinal claro de que um especialista deve ser chamado é a presença de vazamentos significativos. Enquanto pequenos vazamentos de ar podem, às vezes, ser tratados de forma improvisada, grandes vazamentos indicam problemas sérios no sistema de vedação ou em linhas de ar comprimido. Tentar consertar vazamentos substanciais sem a devida experiência pode levar a complicações adicionais, portanto, em casos de vazamento grave, é sempre melhor consultar um profissional qualificado.
Além disso, a ocorrência de ruídos anormais é um fator a ser considerado. Se o compressor começa a fazer barulhos estranhos, como rangidos, zumbidos ou batidas, isso pode ser um indicativo de componentes internos danificados ou desalinhados. Esses problemas muitas vezes requerem desmontagem e reavaliação por um técnico que possa identificar a causa e realizar os reparos necessários. Ignorar esses sinais pode levar a danos mais severos e dispendiosos.
Outro motivo válido para chamar um especialista é a subida de temperatura durante a operação. Compressores de ar têm limites operacionais de temperatura e, se o seu equipamento estiver superaquecendo, pode estar em risco de falha catastrófica. Em vez de tentar lidar com o problema sozinho, entrar em contato com um técnico profissional pode ajudar a diagnosticar a causa do superaquecimento e a implementar soluções corretivas de forma eficaz e segura.
Se você frequentemente se depara com falhas no sistema elétrico, isso também é um sinal claro de que um especialista deve ser chamado. Problemas como fiações desgastadas, conexões soltas, ou falhas em componentes eletrônicos são complexos e arriscados para serem tratados por amadores. Um especialista em manutenção pode inspecionar o sistema elétrico, fazer reparos e garantir que o compressor funcione de maneira segura e eficaz, evitando riscos de choque elétrico ou incêndio.
A necessidade de calibração deve também ser um ponto a considerar. Às vezes, equipamentos desenvolvem desvios nas leituras de pressão ou outros parâmetros operacionais. Se a calibragem não é parte do seu conhecimento técnico, um especialista pode realizar essa tarefa usando ferramentas apropriadas para restaurar o compressor à sua eficiência ideal.
Se o seu compressor apresenta elevados custos operacionais, isso pode também ser um indicativo de que algo não está certo. Um especialista pode avaliar se os custos elevados são causados por falhas de eficiência no compressor, como vazamentos, filtros entupidos ou problemas de lubrificação. A auditoria do sistema pode identificar falhas que levam a um uso excessivo de energia e soluções para corrigi-las.
Por outro lado, a necessidade de manutenção pode ser provocada por modificações no ambiente de operação. Se o compressor foi transferido para um ambiente diferente, pode ser necessário adaptá-lo às novas condições. Chamando um especialista, você pode garantir que seu compressor esteja adequado às novas configurações e funcionamento eficaz sob as novas circunstâncias.
Outra razão para buscar assistência profissional é se você não tem um registro de manutenção adequado. Se o histórico de manutenções é confuso ou inexistente, pode ser arriscado continuar operando o compressor. Um especialista pode ajudar a auditar a situação, realizar manutenções pendentes, documentar corretamente os serviços e ajudar a estabelecer um cronograma preventivo adequado.
Por último, em caso de dúvida ou incerteza, não hesite em buscar a ajuda de um especialista. Se você não está seguro sobre a gravidade do problema ou sobre como proceder, é sempre melhor conversar com um profissional. Muitas vezes, as consultas iniciais podem ajudar a esclarecer a situação e decidir se a intervenção é necessária. Além disso, isso pode criar um relacionamento de longo prazo com um especialista, que pode se tornar um recurso valioso para futuras manutenções e cuidados com o equipamento.
Em resumo, saber quando chamar um especialista em manutenção é fundamental para a eficiência e durabilidade do compressor. Ao reconhecer sinais como problemas de desempenho, vazamentos, ruídos anormais, superaquecimento, falhas elétricas e custos operacionais elevados, você pode prevenir danos maiores e garantir que seu equipamento continue funcionando sem problemas. Lembre-se, ao agir rapidamente e consultar especialistas quando necessário, você não apenas protege seu investimento, mas também assegura a continuidade das operações industriais.
Em suma, a manutenção preventiva em compressores parafuso é uma prática indispensável para garantir que esses equipamentos operem com máxima eficiência e segurança. Ao longo deste artigo, discutimos a importância desta abordagem e os benefícios que ela proporciona, como a redução de custos operacionais, aumento da produtividade e a prolongação da vida útil do compressor. Também abordamos a frequência ideal para a realização das manutenções, os sinais que indicam a necessidade de intervenção, e casos específicos que exigem a ajuda de especialistas. Com um planejamento adequado e atenção constante aos requisitos de manutenção, você pode assegurar que seu compressor funcione sempre em condições ideais, minimizando interrupções e maximizando a eficiência. Não hesite em implementar essas práticas para garantir o desempenho contínuo e confiável do seu equipamento.