Manutenção Preventiva de Compressores: Dicas Essenciais
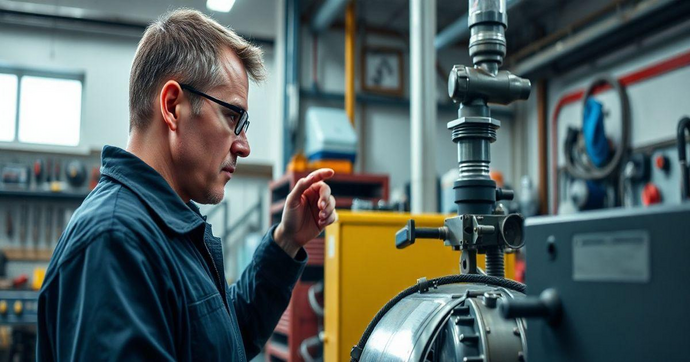
Por: Larissa - 29 de Dezembro de 2024
Manutenção preventiva compressor é uma prática crucial para garantir o funcionamento ideal desse equipamento vital em diversas indústrias. Ao realizar manutenções regulares, é possível evitar falhas inesperadas, aumentar a vida útil do compressor e melhorar sua eficiência operacional. Neste artigo, você encontrará dicas valiosas sobre a importância da manutenção preventiva, técnicas eficazes e um checklist para ajudar a manter seu compressor sempre em ótimo estado. Continue lendo e descubra como cuidar melhor do seu equipamento!
Importância da Manutenção Preventiva em Compressores
A manutenção preventiva em compressores é um aspecto fundamental para garantir a eficiência e a durabilidade desses equipamentos. Como grande parte dos processos industriais depende do funcionamento adequado dos compressores, qualquer falha pode resultar em prejuízos significativos. Neste contexto, entender a importância da manutenção regular é essencial para evitar problemas futuros.
Um dos principais objetivos da manutenção preventiva é minimizar o risco de quebras inesperadas. Ao realizar inspeções regulares, é possível identificar desgastes e falhas antes que se tornem críticos. Isso não apenas protege o equipamento, mas também garante que haja continuidade nas operações. Quando um compressor falha, a parada na produção pode levar a um atraso significativo, o que impacta diretamente o lucro da empresa.
A manutenção preventiva também contribui para a saúde do compressor a longo prazo. Compressores que recebem cuidados adequados tendem a ter uma vida útil mais longa, o que significa menos necessidade de substituições. Isso é particularmente importante em setores onde o Aluguel de compressor de ar é uma opção frequente devido à necessidade de equipamentos em diferentes projetos ou períodos sazonais. Equipamentos bem mantidos são menos propensos a falhas e podem ser alugados com confiança, sabendo que estão em condições excelentes.
A eficiência energética também é um ponto a ser considerado. Compressores que não são mantidos corretamente podem operar com ineficiência, consumindo mais energia do que o necessário. Isso não só aumenta os custos operacionais, mas também pode impactar negativamente o meio ambiente. Práticas de manutenção preventiva ajudam a garantir que os compressores funcionem em sua capacidade ideal, contribuindo para uma operação mais sustentável.
Outro aspecto importante é a segurança. Compressores que não recebem a devida atenção podem apresentar riscos significativos, como vazamentos de ar ou falhas estruturais. A manutenção preventiva permite que os operadores identifiquem problemas de segurança antes que eles se tornem perigosos. Isso não apenas protege os trabalhadores, mas também ajuda a evitar possíveis danos à propriedade e a equipamentos adjacentes.
Além disso, a manutenção preventiva proporciona a oportunidade para treinar a equipe. Quando as equipes realizam inspeções regulares e procedimentos de manutenção, elas se tornam mais familiarizadas com o funcionamento dos compressores. Isso não só aumenta a eficiência durante as operações normais, mas também capacita os funcionários a agir rapidamente em caso de emergências.
As empresas que adotam uma política de manutenção preventiva frequentemente descobrem que os custos associados a essa prática são, na verdade, investimentos. Os gastos antecipados com manutenção preventiva são significativamente menores do que os custos de reparação de um compressor quebrado. Assim, a manutenção não deve ser vista apenas como uma despesa, mas como uma estratégia essencial para a sustentabilidade e o crescimento do negócio.
Por fim, a manutenção preventiva contribui para a manutenção do valor de ativos. Compressores bem mantidos têm uma valorização melhor no mercado. Quando chega o momento de vender ou alugar o equipamento, a condição e a eficiência de um compressor bem cuidado são atrativos para compradores e locatários, aumentando assim o retorno sobre o investimento inicial.
Em resumo, a manutenção preventiva em compressores é vital para garantir a operação eficiente de qualquer negócio que dependa deste tipo de equipamento. Ela não apenas reduz o risco de falhas, mas também aumenta a vida útil do equipamento, melhora a eficiência energética e garante a segurança dos trabalhadores. Portanto, dedicar tempo e recursos para implementar uma estratégia de manutenção preventiva é, sem dúvida, uma das melhores decisões que uma empresa pode fazer.
Tipos de Compressores e suas Especificidades
Os compressores são equipamentos fundamentais em muitos setores industriais, sendo responsáveis pela compressão de ar ou gás para diversas aplicações. Contudo, existem diferentes tipos de compressores, cada um com características específicas que atendem a necessidades distintas. Neste conteúdo, exploraremos os principais tipos de compressores, suas especificidades e indicações de uso.
Um dos tipos mais comuns de compressores é o compressor de deslocamento positivo. Este dispositivo funciona capturando uma quantidade fixa de ar ou gás em um espaço limitado e, em seguida, reduzindo esse espaço, o que resulta no aumento da pressão. Esses compressores costumam ser utilizados em aplicações que necessitam de alta pressão em um volume menor de ar. Os compressores de pistão, que são uma subcategoria de deslocamento positivo, são muito populares e comuns em oficinas e pequenas indústrias devido à sua robustez e capacidade de fornecer pressão adequada para muitas ferramentas pneumáticas.
Os compressores de parafuso são outra opção amplamente utilizada, especialmente em ambientes industriais. Este tipo utiliza dois rotores em espiral que se movem um em relação ao outro. À medida que o ar é sugado, ele é comprimido entre os rotores, gerando ar comprimido de forma contínua e eficiente. Os compressores de parafuso são conhecidos por sua eficiência energética e são ideais para aplicações que exigem um fluxo constante de ar comprimido, como em processos de montagem e fabricação. A locação de compressores de ar desse tipo é uma excelente escolha para empresas que precisam de flexibilidade em sua operação, permitindo ajustar a capacidade do ar comprimido de acordo com a demanda.
Outro segmento de compressores é o dos compressores centrífugos. Estes utilizam um rotor para acelerar o ar ou o gás, que é então direcionado para um difusor, onde a pressão é aumentada. Devido à sua capacidade de manipular grandes volumes de ar, os compressores centrífugos são frequentemente usados em aplicações de grande escala, como na indústria petroquímica e em usinas de energia. A vantagem desse tipo de compressor é anotar que, embora seja mais caro, ele pode oferecer operação eficiente e contínua em grandes capacidades de produção.
Além dos compressores de deslocamento positivo e centrífugos, existem compressores de diafragma. Esses compressores são particularmente úteis em aplicações que requerem alta pureza do ar comprimido, como em laboratórios e processos farmacêuticos. O ar é comprimido através de um diafragma flexível que se move para frente e para trás, criando pressão. Essas unidades têm a vantagem de não contaminar o ar comprimido, garantindo a integridade dos processos industriais e laboratoriais que dependem de ar puro.
Os compressores de ar portátil também são uma categoria importante. Geralmente utilizados em aplicações temporárias ou móveis, esse tipo inclui modelos pequenos e leves, projetados para facilitar o transporte. Eles são ideais para uso em canteiros de obras, jardinagem e atividades que requerem ferramenta pneumática em locais remotos. Por meio da Locação de compressores de ar, os empreendedores podem obter equipamentos adequados para suas necessidades sem altos investimentos iniciais.
Para selecionar o compressor mais adequado, é necessário considerar vários fatores, incluindo a aplicação específica, a quantidade de ar comprimido necessária, a pressão desejada e a eficiência energética. Além disso, é fundamental verificar a manutenção e a durabilidade dos equipamentos, pois isso impactará diretamente a operação e os custos a longo prazo.
Outro fator importante a ser considerado é o nível de ruído gerado pelo compressor. Em ambientes de trabalho sensíveis ao ruído, como hospitais ou escritórios, compressores com níveis de decibéis mais baixos são preferíveis. Existem versões silenciosas de diversos tipos de compressores disponíveis no mercado, que podem atender a essas necessidades específicas sem comprometer a eficiência.
Por fim, a escolha do tipo de compressor deve alinhar-se com os objetivos operacionais da empresa. Analisando e compreendendo as especificidades de cada tipo, as organizações podem maximizar sua eficiência operacional, minimizar custos e garantir um fluxo constante de ar comprimido para suas atividades produtivas. Seja você um pequeno empresário ou uma grande indústria, há um compressor ideal para atender às suas demandas específicas.
Principais Sinais de Falhas em Compressores
Identificar sinais de falhas em compressores é crucial para garantir o funcionamento eficiente e seguro dos equipamentos. Muitas vezes, os problemas podem ser detectados em estágios iniciais, evitando a necessidade de reparos dispendiosos e prolongadas paradas na produção. Neste artigo, vamos abordar os principais sinais de falhas em compressores e a importância de estar atento a esses sintomas.
Um dos sinais mais comuns de falha é a diminuição da capacidade de pressão. Se você notar que o compressor não está atingindo a pressão desejada ou que leva mais tempo para chegar a ela, pode ser um indicativo de que algo não está funcionando corretamente. Isso pode ser causado por vazamentos, problemas nos componentes internos do compressor ou filtros entupidos. Verifique se as mangueiras e conexões estão em boas condições, pois vazamentos de ar podem reduzir a eficiência do equipamento.
Outro sinal de alerta é o aumento do ruído durante a operação. Compressores normalmente operam em níveis de ruído proporcionais à sua capacidade, mas qualquer alteração significativa no som deve ser investigada. Ruídos excessivos podem indicar problemas com os rolamentos, necessidade de lubrificação, ou até falhas estruturais internas. É importante estar atento a sons incomuns, como chiados, estalos ou vibrações, pois podem ser indícios de que o compressor está perto de falhar.
Além disso, a alteração na temperatura de operação é um indicador importante a ser monitorado. Se o compressor estiver operando em temperaturas mais altas do que o normal, ou se você perceber a presença de fumaça, isso pode sinalizar superaquecimento, que pode ser causado por falta de manutenção ou problemas com o sistema de refrigeração. O superaquecimento não só diminui a eficiência do equipamento, como pode levar a danos irreparáveis. Para evitar essa situação, é fundamental realizar a manutenção compressor de ar regularmente.
A ocorrência de vibrações excessivas durante a operação também é um sinal claro de problemas. Um compressor que vibra mais do que o normal pode estar desbalanceado ou ter componentes soltos, como parafusos ou suportes. Essas vibrações podem danificar partes do compressor e aumentar o desgaste. Se as vibrações forem mais intensas, é essencial interromper a operação e investigar a causa imediatamente.
Outro sintoma de possíveis falhas é o alto consumo de energia. Se do nada você perceber que a fatura de energia aumenta exponencialmente, isso pode ser um indicativo de que o compressor não está operando de maneira eficiente. Fatores como filtros obstruídos, vazamentos ou falhas mecânicas podem levar a um maior consumo de energia, assim como a necessidade de mais tempo de funcionamento para atingir a mesma produção. Esse aumento nos custos pode impactar significativamente o orçamento operacional de uma empresa.
A presença de água no sistema de ar comprimido é outro sinal que não deve ser ignorado. A umidade no ar comprimido pode causar corrosão e danos aos equipamentos que utilizam o ar comprimido, além de afetar a qualidade do produto final. Se você notar a presença de água, pode ser um sinal de que o separador de água do compressor não está funcionando adequadamente ou que há falhas nos filtros. É fundamental manter o sistema de drenagem do compressor em bom estado para evitar a formação de umidade.
Os indicadores no painel do compressor também fornecem informações valiosas sobre o estado do equipamento. Fique atento a luzes de alerta ou medidores que estejam fora dos limites normais. Muitos compressores modernos são equipados com sistemas de monitoramento que podem alertar os operadores sobre condições anormais de funcionamento. Estar atento a estes sinais pode facilitar a identificação de problemas antes que se tornem situações mais sérias.
Por fim, a falta de manutenção regular é um sinal de que o equipamento pode falhar. Se a manutenção preventiva não estiver sendo realizada, a probabilidade de problemas aumenta significativamente. As empresas devem priorizar o cronograma de manutenção para evitar o desgaste prematuro dos componentes do compressor. Um mantido adequadamente não só desempenha melhor, mas também é menos suscetível a falhas.
Em resumo, reconhecer os principais sinais de falhas em compressores é fundamental para a operação eficiente e segura dos equipamentos. Desde a diminuição da capacidade de pressão até a alteração nas condições de operação, cada um desses sinais deve ser levado a sério. Para garantir que seu compressor funcione da melhor maneira possível, invista em manutenções preventivas e fique sempre atento a qualquer alteração no desempenho do equipamento.
Periodicidade Recomendada para a Manutenção
A manutenção regular de compressores é um aspecto essencial para garantir a eficiência, segurança e durabilidade desses equipamentos. A periodicidade recomendada para a manutenção pode variar dependendo do tipo de compressor, das condições de operação e da intensidade de uso. Neste artigo, discutiremos as diretrizes gerais sobre a frequência de manutenção e a importância de criar um cronograma adequado.
Em geral, os fabricantes de compressores fornecem recomendações específicas sobre a frequência de manutenção. No entanto, algumas diretrizes universais podem ser observadas para maximizar a vida útil e o desempenho do equipamento. Para compressores que operam em ambientes normais, a manutenção deve ser realizada a cada 1.000 horas de operação ou, pelo menos, uma vez por ano. Isso inclui uma série de atividades de inspeção e lubrificação que são cruciais para o funcionamento adequado do equipamento.
A manutenção preventiva deve incluir a verificação de todos os componentes principais do compressor, como filtros de ar, óleos, correias e mangueiras. Por exemplo, um compressor de ar parafuso 30 hp pode exigir um esquema de manutenção um pouco diferente de outros modelos, devido às suas especificidades de operação e design. A inspeção e a troca de peças desgastadas ou com defeito pode prevenir problemas futuros e garantir que o compressor opere em níveis ideais de eficiência.
Além das recomendações do fabricante, a quantidade de uso e as condições ambientais são fatores críticos a serem considerados. Compressores que operam em ambientes com alta presença de poeira, umidade ou temperatura extrema podem exigir manutenções mais frequentes. Por exemplo, ambientes industriais pesados podem exigir manutenção a cada 500 horas de operação, enquanto compressores utilizados em aplicações mais leves podem se beneficiar de um intervalo maior entre as manutenções.
A troca de óleo é uma parte importante da manutenção de compressores. O óleo responsável pela lubrificação dos componentes internos deve ser trocado regularmente, conforme as orientações do fabricante. O não cumprimento dessa diretriz pode resultar em aumento do atrito e, consequentemente, em falhas mecânicas. Além do óleo, os filtros de ar e óleo devem ser verificados e substituídos conforme necessário. Filtros entupidos podem restringir o fluxo de ar, reduzindo a eficiência do compressor.
Outro aspecto a ser considerado é a verificação do sistema de resfriamento. Os compressores geram calor durante a operação, e um sistema de resfriamento inadequado pode levar a sérios problemas de superaquecimento. A manutenção deve envolver a limpeza e a inspeção dos componentes do sistema de resfriamento, como radiadores e ventiladores. Em casos de operação em ambientes quentes ou áreas com alta temperatura, poderá ser necessário realizar manutenção na frequência de 250 a 500 horas de operação.
Além das manutenções programadas, é essencial estar atento a qualquer alteração no comportamento do compressor. Ruídos incomuns, vibrações excessivas ou mudanças na pressão de operação podem indicar que uma manutenção não programada deve ser realizada imediatamente. Quanto mais cedo o problema for identificado, menor será o impacto na operação e nos custos associados à solução. Um cronograma de manutenção eficaz deve incluir não apenas as manutenções programadas, mas também um protocolo para lidar com possíveis emergências.
Esse tipo de gestão pode ser feito através de softwares de gerenciamento de ativos que auxiliam na criação de lembretes e cronogramas de manutenção. Essa tecnologia pode ajudar a manter registros das manutenções realizadas e das peças trocadas, permitindo uma análise mais aprofundada do desempenho ao longo do tempo. A implementação de tais ferramentas pode proporcionar maior controle sobre o status do compressor e garantir que nenhuma atividade fundamental seja negligenciada.
Uma dica é propor uma rotina de manutenção aos operadores do compressor, educando-os sobre a importância de relatar alterações de desempenho assim que elas forem percebidas. Isso cria uma cultura de conservação e atenção em relação aos equipamentos, facilitando a identificação precoce de potenciais falhas.
Por fim, a periodicidade recomendada para a manutenção de compressores deve ser visualizada não apenas como uma questão de cumprimento de regulamentos, mas como um investimento na eficiência e na operação do equipamento. Uma abordagem rigorosa e consistente de manutenção ajuda a garantir o máximo desempenho, segurança e durabilidade, além de proporcionar paz de espírito, sabendo que o compressor está sempre em condições ideais de funcionamento.
Checklist de Manutenção Preventiva para Compressores
A manutenção preventiva é fundamental para garantir a eficiência e a durabilidade dos compressores. Um checklist de manutenção preventiva bem estruturado pode ajudar a identificar problemas em potencial antes que se tornem falhas graves, minimizando interrupções na produção e custos com manutenção emergencial. Neste artigo, apresentaremos um checklist abrangente que pode ser seguido para a manutenção de compressores.
O primeiro item do checklist deve ser a verificação dos níveis de lubrificação. É vital que o óleo do compressor esteja no nível adequado, pois a lubrificação insuficiente pode causar desgaste prematuro e até falhas mecânicas. Verifique a qualidade do óleo; se estiver escuro ou contaminado, é hora de fazer a troca. Recomenda-se substituir o óleo conforme a periodicidade indicada pelo fabricante, geralmente a cada 1.000 horas de operação.
Além da lubrificação, a inspeção dos filtros de ar é um passo crucial. Filtros obstruídos reduzem a eficiência do compressor, podendo causar superaquecimento e perda de pressão. Limpe ou substitua os filtros de ar de acordo com o cronograma de manutenção. Dependendo do ambiente em que o compressor opera, pode ser necessário verificar os filtros com mais frequência, especialmente em áreas com alta concentração de poeira ou partículas.
A próxima etapa envolve a verificação das mangueiras e conexões. Certifique-se de que não há vazamentos, rachaduras ou sinais de desgaste nas mangueiras. Vazamentos podem resultar na perda de pressão e eficiência, além de causar danos ao ambiente de trabalho. Realize inspeções visuais e, sempre que possível, teste a pressão das mangueiras para garantir que estejam em boas condições.
Além disso, a verificação dos componentes elétricos é uma parte crucial da manutenção preventiva. Inspecione os cabos, conexões e o painel elétrico em busca de sinais de desgaste ou danos. Fios soltos ou danificados podem causar falhas elétricas, colocando o compressor em risco. A realização de medições de tensão e corrente pode ajudar a garantir que o sistema elétrico esteja funcionando corretamente.
Outro item importante no checklist é a limpeza do radiador e do sistema de resfriamento. Compressores que operam por períodos extensos geram calor acumulado, e um sistema de resfriamento eficaz é fundamental para mantê-los operando em condições ideais. Limpe as grelhas e os dissipadores de calor para garantir a circulação de ar adequada. A vazão de ar correta pode ser verificada através de testes de temperatura, que ajudam a identificar qualquer problema no sistema de resfriamento.
A manutenção preventiva também inclui verificar os níveis de contaminação do ar comprimido. Isso é particularmente importante para compressores que fornecem ar para processos sensíveis, como em indústrias alimentícias e farmacêuticas. O uso de separadores de água e filtros adicionais pode ajudar a manter a qualidade do ar comprimido. Regularmente, colete amostras de ar e analise sua pureza para garantir que os padrões estejam sendo atendidos.
O balanceamento das peças móveis é outra parte essencial da manutenção. O desbalanceamento pode causar vibrações e aumentar o desgaste dos componentes. Verifique o alinhamento das partes móveis e o desgaste dos rolamentos. Componentes como correias e polias devem ser inspecionados e substituídos se apresentarem sinais de danos ou ruído excessivo durante a operação.
Documentar as manutenções realizadas é uma prática valiosa. Mantenha um registro detalhado de todas as inspeções, trocas de óleo, substituições de peças e quaisquer anotações dos operadores. Essa documentação não apenas ajuda a manter um histórico da saúde do compressor, mas também pode auxiliar na fiscalização e no planejamento de futuras manutenções. Quando bem organizado, esse registro se torna uma ferramenta poderosa para a gestão de ativos de equipamentos.
A realização de treinamentos periódicos com a equipe também é essencial. Garanta que os operadores estejam cientes dos procedimentos de manutenção preventiva e saibam como identificar sinais de falhas. Treinamentos regulares melhoram a abordagem de segurança e eficiência e ajudam a criar uma cultura de responsabilidade em relação ao uso e à manutenção dos compressores.
Por fim, estar preparado para a manutenção não programada é tão importante quanto as manutenções programadas. Sempre que um operador notar um comportamento atípico do compressor, como ruídos estranhos ou quedas de pressão, deve haver um protocolo claro a seguir, que possa envolver a interrupção imediata da operação e a solicitação de uma manutenção urgente.
Em resumo, um checklist de manutenção preventiva para compressores é uma ferramenta vital para garantir o funcionamento eficiente e seguro dos equipamentos. Seguindo essas etapas e mantendo vigilância constante, empresas podem reduzir riscos de falhas, garantir a continuidade da produção e prolongar a vida útil de seus compressores. Montar, revisar e executar este checklist regularmente garantirá que seu compressor continue a operar em níveis ideais.
Técnicas e Ferramentas para Manutenção Eficiente
A manutenção eficiente de compressores é fundamental para garantir o desempenho ideal e a durabilidade dos equipamentos. Ao adotar técnicas eficazes e utilizar as ferramentas adequadas, é possível otimizar o processo de manutenção, reduzindo custos e minimizando o tempo de inatividade. Neste artigo, abordaremos algumas das principais técnicas e ferramentas que podem ser utilizadas para uma manutenção eficiente de compressores.
Uma das técnicas mais eficazes é a manutenção preventiva, que envolve a realização de inspeções regulares e a execução de tarefas de manutenção programadas. A ideia é identificar e corrigir problemas antes que se tornem falhas mais graves. Para implementar a manutenção preventiva, é crucial criar um cronograma de manutenção, que pode incluir verificações diárias, semanais e mensais. Este cronograma deve ser customizado com base nas recomendações do fabricante e nas condições de operação do compressor.
Para registrar o desempenho do compressor e monitorar seu estado, a utilização de ferramentas de software de gerenciamento de ativos pode ser muito benéfica. Esses softwares permitem que as empresas rastreiem as horas de funcionamento, programem manutenções e mantenham um histórico detalhado dos serviços realizados. Isso ajuda a tomar decisões informadas sobre quando realizar a manutenção e quais peças precisam ser substituídas.
A inspeção visual é uma técnica simples, mas extremamente eficaz na manutenção de compressores. Durante as inspeções, os operadores devem observar a presença de corrosão, vazamentos, sinais de desgaste e quaisquer componentes que estejam fora do lugar. Uma verificação visual minuciosa pode revelar problemas que podem ser corrigidos antes que causem falhas sérias. Além disso, documentar essas observações pode ser útil para monitorar padrões de desgaste ao longo do tempo.
Outra técnica importante é a utilização de tecnologias de monitoramento de condições. Com o avanço da tecnologia, sensores de vibração, temperatura e pressão podem ser instalados nos compressores para monitorar seu desempenho em tempo real. Esses sensores ajudam a identificar anomalias que podem indicar problemas no equipamento, permitindo que os operadores atuem rapidamente para corrigir qualquer falha antes que ela se agrave. Essa abordagem também ajuda a maximizar a eficiência do compressor e a reduzir os custos de operação.
As ferramentas de diagnóstico são indispensáveis para a manutenção eficiente. Estas ferramentas podem incluir medidores de pressão, manômetros e analisadores de gás. Com esses equipamentos, os técnicos podem avaliar rapidamente o estado do compressor e identificar problemas. Por exemplo, manômetros podem ser usados para monitorar a pressão de entrada e saída do compressor, enquanto analisadores de gás podem diagnosticar a qualidade do ar comprimido.
Além de ferramentas de diagnóstico, equipamentos de limpeza também são essenciais para a manutenção de compressores. Filtros de ar e componentes internos devem ser mantidos limpos para garantir que o compressor opere com eficiência. O uso de aspiradores industriais e limpadores de alta pressão pode ajudar a remover poeira e detritos que se acumulam ao redor do compressor, evitando obstruções e melhora na circulação de ar.
A troca regular de componentes, como os filtros de ar e óleo, é uma parte importante da manutenção preventiva. O uso de ferramentas adequadas, como chaves de boca e chaves de fenda, pode facilitar esse processo e garantir que as peças sejam substituídas de maneira correta. Estar atento às orientações do fabricante sobre a frequência da troca de filtros é essencial para garantir a qualidade do ar comprimido e a eficiência do compressor.
A formação e capacitação dos operadores também são fundamentais para uma manutenção eficaz. Os operadores que conhecem bem o funcionamento do compressor e a importância da manutenção preventiva são mais propensos a identificar problemas rapidamente e a realizar intervenções preventivas. Portanto, investir em treinamentos e capacitações regulares pode melhorar consideravelmente a eficiência da manutenção.
Vale ressaltar a importância de seguir as instruções do fabricante ao utilizar qualquer ferramenta ou técnica de manutenção. Cada modelo de compressor pode ter necessidades específicas, e o não cumprimento das diretrizes pode resultar em danos ao equipamento. Além disso, a segurança dos operadores deve ser sempre priorizada, utilizando Equipamentos de Proteção Individual (EPIs) apropriados durante qualquer atividade de manutenção.
Em resumo, a adoção de técnicas e ferramentas adequadas é crucial para garantir a manutenção eficiente de compressores. A combinação de manutenção preventiva com o uso de tecnologias de monitoramento, ferramentas de diagnóstico e práticas de limpeza garante que os compressores operem em sua máxima eficiência e segurança. Investir nessas técnicas e ferramentas não somente reduz custos operacionais, mas também prolonga a vida útil dos equipamentos, garantindo um funcionamento contínuo e produtivo.
Benefícios da Manutenção Preventiva para Empresa
A manutenção preventiva é uma estratégia essencial para empresas que dependem de equipamentos como compressores para suas operações diárias. Embora muitas organizações possam enxergar a manutenção preventiva apenas como uma despesa, ela pode trazer uma série de benefícios significativos que vão além da simples preservação do equipamento. Neste artigo, exploraremos os principais benefícios da manutenção preventiva para empresas e como ela pode impactar positivamente a eficiência operacional e a rentabilidade.
Um dos principais benefícios da manutenção preventiva é a redução de custos operacionais. Ao realizar manutenções programadas e regulares, as empresas podem evitar falhas inesperadas que, geralmente, exigem reparos caros e podem levar a interrupções significativas na produção. Equipamentos bem mantidos têm menor probabilidade de quebrar e, portanto, geram menos custos com consertos emergenciais. Isso se traduz em economia a longo prazo, permitindo que os recursos financeiros sejam redirecionados para outras áreas que possam trazer mais retorno ao negócio.
Outro aspecto importante da manutenção preventiva é o aumento da eficiência operacional. Equipamentos que recebendo cuidados adequados tendem a operar de maneira mais eficiente. Por exemplo, um compressor que está bem lubricado e devidamente ajustado consome menos energia e proporciona um desempenho superior. Isso não apenas melhora a produtividade, mas também minimiza o impacto ambiental, uma vez que uma operação mais eficiente resulta em menor consumo de energia e, consequentemente, menor emissão de gases poluentes.
A manutenção preventiva também contribui para a longevidade dos equipamentos. Compressores e outras máquinas pesadas, quando mantidos de maneira adequada, podem durar significativamente mais do que aqueles que não recebem cuidados regulares. Essa durabilidade é crítica para empresas que são dependentes de seus equipamentos para a produção e entrega de serviços. A longo prazo, um investimento em manutenção preventiva pode significar uma maior vida útil dos equipamentos, resultando em menor necessidade de compras frequentes para reposição.
Adicionalmente, a manutenção preventiva ajuda a garantir a segurança no ambiente de trabalho. Compressores que não são bem mantidos podem representar riscos à segurança, como vazamentos de ar ou falhas que podem levar a acidentes. Através de uma manutenção regular, os operadores podem identificar e corrigir problemas antes que eles se tornem situações perigosas. Isso não somente protege os trabalhadores, mas também reduz a possibilidade de custos adicionais associados a acidentes de trabalho, que podem incluir indenizações e interrupções nas atividades.
Um benefício frequentemente negligenciado da manutenção preventiva é a melhoria na qualidade do produto final. Em muitas indústrias, a qualidade do ar comprimido é fundamental para garantir que o produto atendenda padrões exigidos. Compressores bem mantidos oferecem ar comprimido limpo e seco, o que resulta em produtos de melhor qualidade. Isso é especialmente importante em setores sensíveis, como os de alimentos e farmacêutico, onde a contaminação pode ter consequências graves.
Além disso, a manutenção preventiva pode aumentar a confiabilidade dos equipamentos. Quando um compressor é mantido corretamente, ele opera de forma mais previsível, permitindo que os gestores planejem melhor as suas operações. Essa confiabilidade é fundamental para empresas que operam em ambientes just-in-time, onde a continuidade da produção deve ser garantida. Assim, ao saber que os equipamentos estão em boas condições, as empresas podem se concentrar em suas atividades principais, gerenciando melhor suas equipes e recursos.
Implementar uma estratégia de manutenção preventiva também proporciona uma oportunidade de treinamento e desenvolvimento para os funcionários. Ao capacitá-los para realizar tarefas de manutenção básica, as empresas não só empoderam seus colaboradores, como também fomentam um ambiente de trabalho mais engajado e produtivo. Os funcionários que entendem a importância da manutenção são mais propensos a cuidar do equipamento e a relatar problemas de forma proativa, beneficiando a empresa no geral.
Por fim, vale destacar que a manutenção preventiva pode melhorar a imagem da empresa. Investir em manutenção demonstra um compromisso com a qualidade e a segurança, fatores que são valorizados por clientes e parceiros comerciais. Uma empresa que opera com equipamentos bem mantidos projeta uma imagem de profissionalismo e eficiência, o que pode resultar em mais oportunidades de negócio e maior fidelização de clientes.
Em resumo, os benefícios da manutenção preventiva para empresas são vastos e impactantes. Desde a redução de custos operacionais e o aumento da eficiência até a melhoria da segurança e qualidade dos produtos, investir em uma estratégia de manutenção não é apenas sensato, mas fundamental para a saúde e o sucesso a longo prazo de qualquer empresa que dependa de máquinas e equipamentos. Portanto, adotar a manutenção preventiva como parte integral da estratégia de gestão de ativos é uma decisão inteligente que, sem dúvida, trará resultados positivos!
Quando Chamar um Profissional Especializado?
Em um ambiente industrial onde compressores desempenham um papel crucial nas operações, saber quando chamar um profissional especializado é fundamental para garantir a eficiência e a segurança do equipamento. A manutenção e o reparo de compressores requerem conhecimentos técnicos e habilidades específicas. Portanto, é essencial reconhecer os sinais que indicam que a assistência de um especialista se faz necessária. Neste artigo, discutiremos os principais cenários em que você deve considerar a contratação de um profissional especializado.
Um dos primeiros sinais de que é hora de chamar um profissional é quando há uma queda significativa na eficiência do compressor. Se o equipamento não estiver operando em sua capacidade ideal, resultando em temperaturas excessivas, altos níveis de vibração ou picos de pressão inexplicáveis, essa é uma indicação clara de que um especialista deve ser consultado. Muitas vezes, esses problemas podem ser causados por falhas internas que um operador não pode diagnosticar sem um conhecimento técnico adequado.
Além disso, se o compressor começar a emitir ruídos anormais, como batidas, chiados ou rangidos, isso pode indicar que há um componente interno desgastado ou danificado. Esses sons podem ser sinais de problemas sérios que exigem atenção imediata. Embora você possa realizar algumas inspeções visuais, um técnico especializado terá as ferramentas e o conhecimento necessários para diagnosticar o problema corretamente e evitar falhas catastróficas.
Outro sinal importante a ficar atento é a presença de vazamentos de ar. Se você notar uma redução na pressão do sistema que não pode ser atribuída a um uso elevado, isso pode ser resultado de um vazamento. Vazamentos não apenas comprometem a eficiência operacional, mas também podem levar a custos excessivos de energia. A localização e o reparo de vazamentos podem ser complicados, e um profissional especializado tem a experiência necessária para abordar esses vazamentos de maneira eficaz e eficiente.
A presença de água no ar comprimido também é um alerta. Um compressor que não seja capaz de remover a umidade adequadamente pode resultar em contaminação do sistema, corrosão e danos a ferramentas e maquinários. Se você perceber a presença de água no sistema de ar comprimido, a chamada a um especialista é necessária para garantir que o equipamento esteja limpo e seguro para uso. Essa é uma questão que deve ser tratada rapidamente para evitar danos a longo prazo.
Outra situação em que é fundamental buscar a ajuda de um profissional é quando a manutenção preventiva não está sendo efetiva. Se você está seguindo um cronograma regular de manutenção, mas ainda assim está enfrentando problemas frequentes com o compressor, isso pode indicar que a manutenção não está sendo realizada de maneira adequada ou que há problemas mais sérios por trás disso. Um profissional experimentado pode revisar os procedimentos de manutenção, identificar lacunas e sugerir melhorias.
Além disso, se o seu compressor estiver próximo do fim de sua vida útil, é uma boa ideia consultar um especialista. Um técnico poderá avaliar o estado geral do equipamento e, se necessário, discutir suas opções de substituição. Essa avaliação pode economizar tempo e dinheiro no longo prazo, já que um compressor em fim de vida pode ter um desempenho muito abaixo do ideal e ser sujeito a falhas frequentes.
As condições ambientais também podem requerer a assistência de um profissional especializado. Ambientes de trabalho com alta presença de poeira, umidade ou temperaturas extremas podem causar desgaste acelerado de equipamentos. Se você trabalha em tais condições e não está certo de como manter seu compressor adequadamente, buscar a ajuda de um especialista pode fornecer as melhores práticas e orientações para cuidar de seus equipamentos. Eles poderão recomendar soluções para proteger o compressor e otimizar seu desempenho nessas circunstâncias desafiadoras.
Por último, a falta de conhecimento técnico e a inexperiência são razões válidas para chamar um profissional. Se a equipe de operadores ou manutenção não tem experiência suficiente, isso pode resultar em erros que podem danificar o compressor ou criar condições inseguras. Um técnico qualificado pode fornecer a orientação necessária, além de realizar a manutenção e reparos de maneira adequada e segura.
Em resumo, saber quando chamar um profissional especializado pode agilizar a solução de problemas e garantir que os compressores mantenham sua operação ideal. Ao prestar atenção aos sinais de alertas, como queda de eficiência, ruídos anormais, vazamentos de ar e presença de água, você estará mais preparado para agir rapidamente. Além disso, o suporte de um especialista pode não apenas evitar falhas catastróficas, mas também ajudar a prolongar a vida útil do equipamento e garantir um ambiente de trabalho seguro e produtivo.
Em conclusão, a manutenção preventiva compressor não é apenas uma prática recomendada, mas sim um aspecto essencial para o sucesso e a eficiência das operações em diversas indústrias. Ao investir tempo e recursos em manutenções regulares, você minimiza o risco de falhas inesperadas, aumenta a durabilidade dos equipamentos e otimiza o desempenho geral. Além das dicas e práticas mencionadas, a criação de uma cultura de manutenção dentro da sua organização contribui para a segurança e bem-estar dos funcionários. Portanto, ao seguir as orientações apresentadas, você não só garantirá o funcionamento ideal do seu compressor, mas também poderá colher os benefícios financeiros e operacionais significativos que vêm com um equipamento bem mantido. Cuide do seu compressor e colha os frutos de um desempenho excepcional!